Bikes and Builders of 2024 Bespoked UK (Part 2)
In our second set of coverage Bespoked UK 2024, find several more inspiring stories of small frame builders and makers, including one about a wild frame conversion from Bousif Custom Bikes, the best in show bike from BTR Fabrications, a new “carry” bike from Assembly, bags born from “British Gravel” and more…
PUBLISHED Jul 2, 2024
If you read part one of my 2024 Bespoked UK coverage, you know I love digging into how folks got into making bikes and things for bikes, and how those meager beginnings led to where they are now. These stories are often inspiring, but the reality is that running a small business is hard work, very stressful, and full of uncertainty. You’ve all heard about the bike industry bust after the Covid-19 pandemic boom, right? The reality is that small frame builders and makers feel it too.
One conversation really stands out to me from the many I had at Bespoked UK. Clandestine’s Pi Manson mentioned that, “When you buy a frame from a mid-sized bike company, someone in sales may give a nod when they see the report. When you purchase a bike from a small brand of four or five employees, someone may utter, “Yes!” When you buy a bike from a one-person brand who has their frames made elsewhere, the owner probably proffers a fist shake and a solid “YES!” And when you order a bike from a one-person frame builder who will make that bike, they no doubt raise their fist and shout, ‘YESSS!!’”
Take that to heart as you read the next set of stories below.
Boucif Custom Bikes (BCB) Paratrooper link
Leuven, Belgium
If there was a life of the party at Bespoked UK, it was without a doubt Driss Boucif and his partner in crime Chipo Sikumba. After I wrapped up shooting Alfano and Clandestine first on day one, I spotted these two guys standing beside their giant Leuven banner with nothing more than two bikes propped up on their own kickstands. They were already well into their first beer; I looked at my watch, and it was before noon, so I broke the ice by letting them know that they were one step ahead of the curve. We hit it off immediately and proceeded to set up the BCB Paratrooper for photos. I liked the look of it but had no idea what this bike was all about until mid-shoot as we were chatting.

But before I reveal that little nugget, let’s rewind back to 2011 in Leuven, Belgium. Driss found his way to bicycles by way of mopeds, oddly enough. He was 16 at the time and had a Kawasaki moped that he was obsessed with. “It was the only thing on my mind and all I wanted to do was ride it and make it go faster,” Driss explained. He didn’t care for school but heard about an alternative in Leuven where you could study bicycle, moped, and lawnmower mechanics. “I really didn’t like school and I wasn’t a great student, but that drastically changed when I switched schools… Originally I was only in it for the moped part, but then I discovered the magic of frames and handling. How cool is it when you can be faster than a rider with more horsepower because your bike handles better?”
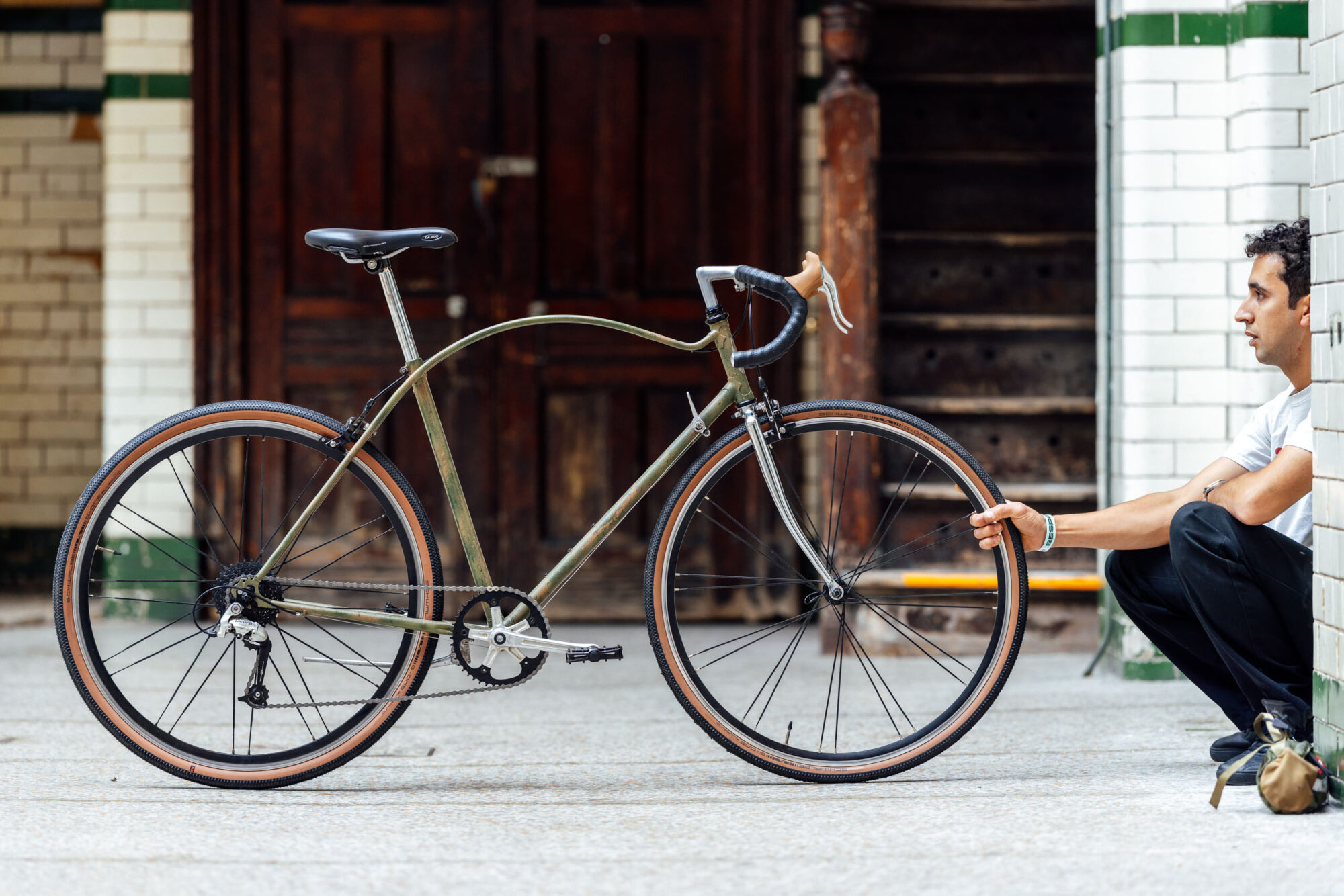
Driss began altering old bicycle frames, which was far more accessible for a 17-year-old than modifying motorcycles. He became fascinated by the variation in handling that small modifications had on existing bikes. Swapping forks completely transformed the feel of a bike; alternating wheel sizes front and rear resulted in a sharper or more stable vibe; steepening the frame’s headtube angle quickened the handling. There were all sorts of easy mods to play with. “There was one that I still do today on most of my bikes: put a skinnier tire in the front, which makes the handling sharper, and a fatter tire in the back to keep it sturdy and withstand wild riding on and off curbs and steps,” Driss added.
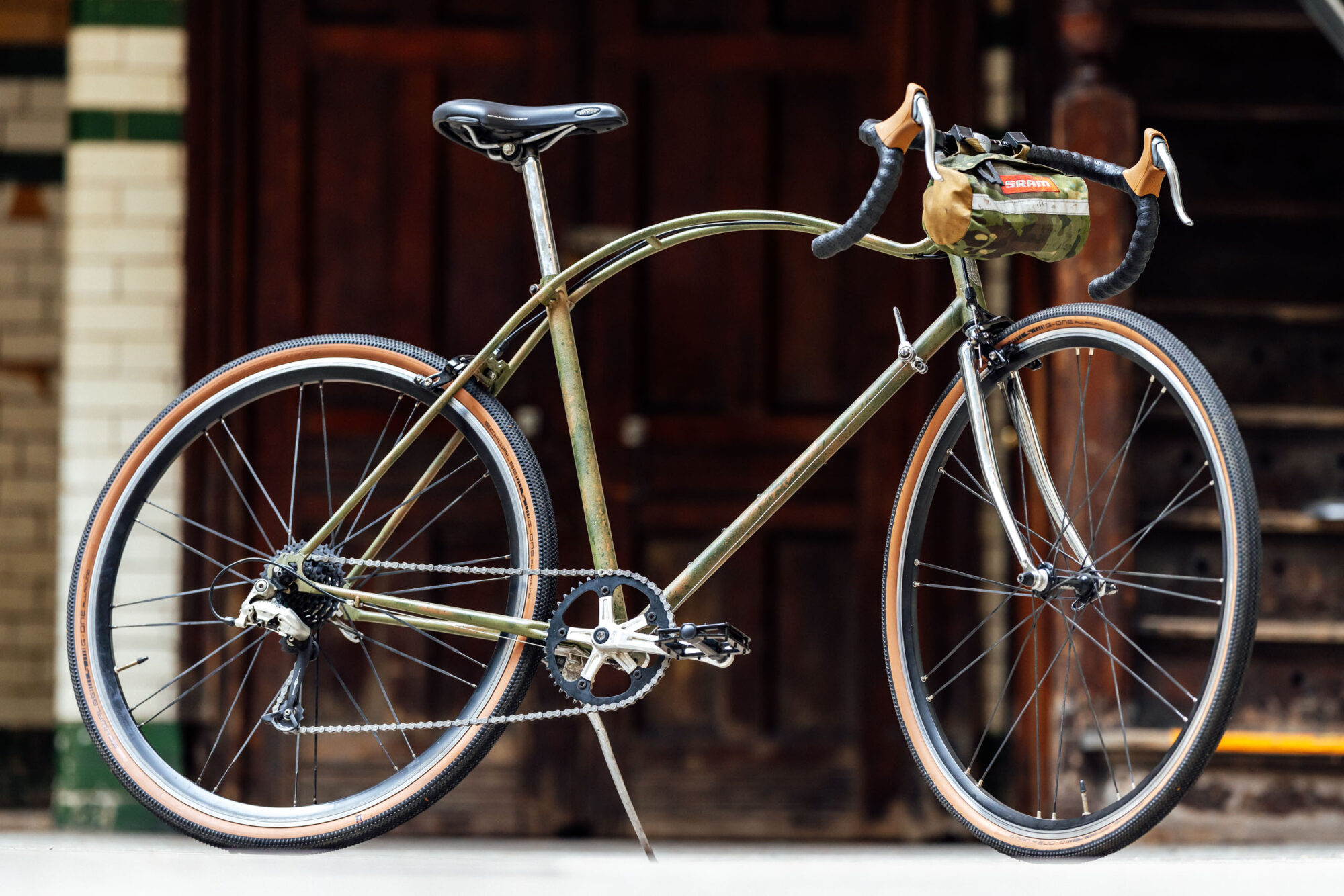
Interestingly, Driss preferred the handling of ’70s or ’80s step-through bikes. “The way you can sweep them through sharp corners and feel the flex… way more feedback than a stiff modern diamond aluminum frame,” Driss explained. “The problem was that I bent them like tacos by riding too hard, going down stairs, or hitting jumps that were a little too much.” That’s when he figured out a recipe to turn those old step-through mixtes into something special. By cutting out the twin tubes, flipping them, and re-welding them in place, the same tubeset becomes a whole lot stronger, “but it still has a bit of flex to it, which is what I love about these bikes.” When the frame is chopped up, Driss could also change the headtube angle, the steepness of the seat tube, and sometimes shorten the chainstays before welding everything into a new creation.
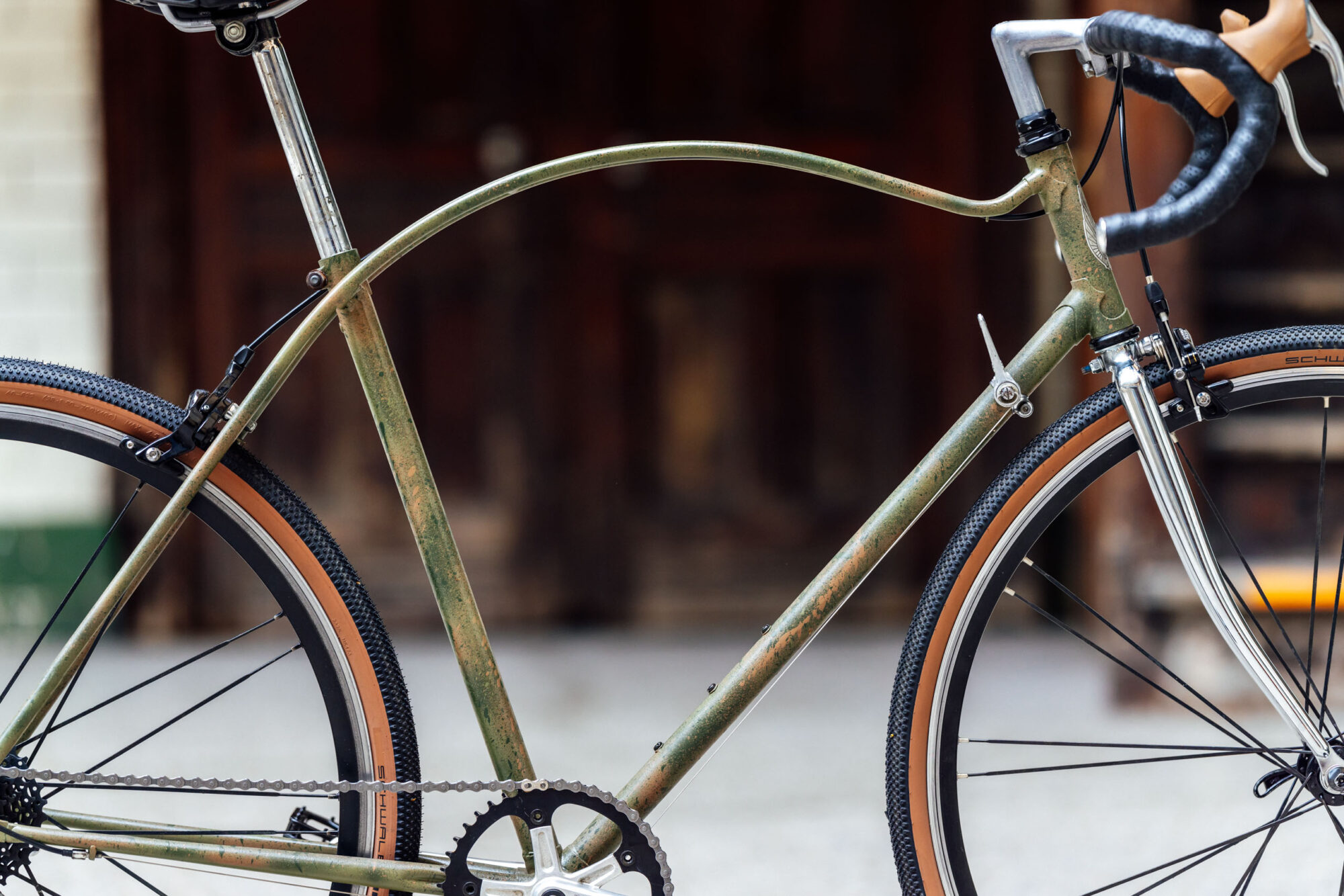
That’s exactly what the BCB Paratrooper is. It began its life as an old ’80s step-through town bicycle that probably brought groceries to someone’s home in a basket at some point in time. This past weekend, it was Driss’s urban assault vehicle that I saw him wheelie around the balcony at one point during the show. It’s one of Boucif Custom Bikes’ classic builds, made to be quick and sturdy, outfitted with rim brakes and a friction shifter on the downtube for simplicity. Driss puts his bikes in their own category: gravel and travel. They’re reliable and tough, so you could travel the world with them, and even if you need repairs, you can find the parts anywhere. As a matter of fact, his friend and customer Chipo Sikumba took one on a long tour last year with a couple of giant panniers, which he admitted were way too overstuffed. In fact you can see a couple BCBs in bikepacking mode on this Instagram post.
After Driss’s studies, he opened a bike shop in Leuven that he now runs full-time. He admits that the people he builds bikes for have greatly impacted the frames he creates. “They are mostly students or other young people, and in Leuven, everyone has at least one bike… it’s the main way of transport, I would say. My clients and I mostly ride in the city, but we also love doing trips and riding gravel,” Driss added. He also mentioned that Leuven is hosting a World Cup gravel race this year and that bikepacking is gaining popularity with his customers. Keep up the great work, Driss! Hopefully, we can catch up again soon. For those interested in seeing more from BCB, be sure to give them a follow on Instagram @boucif_custom_bikes.
Assembly Carry Bike link
London, England
Assembly is a London-based bike company founded by Jim Lowe, a general fabricator and tradesperson who has spent the last 15 years working in the city. Lowe’s journey into building bikes began out of necessity. Recognizing the advantages of using a bike to carry tools and materials to and from job sites, he searched for a suitable cargo bike but couldn’t find one that met his needs. This challenge inspired him to create his own, which eventually landed him the prize for Best Utility Bike here at Bespoked UK.
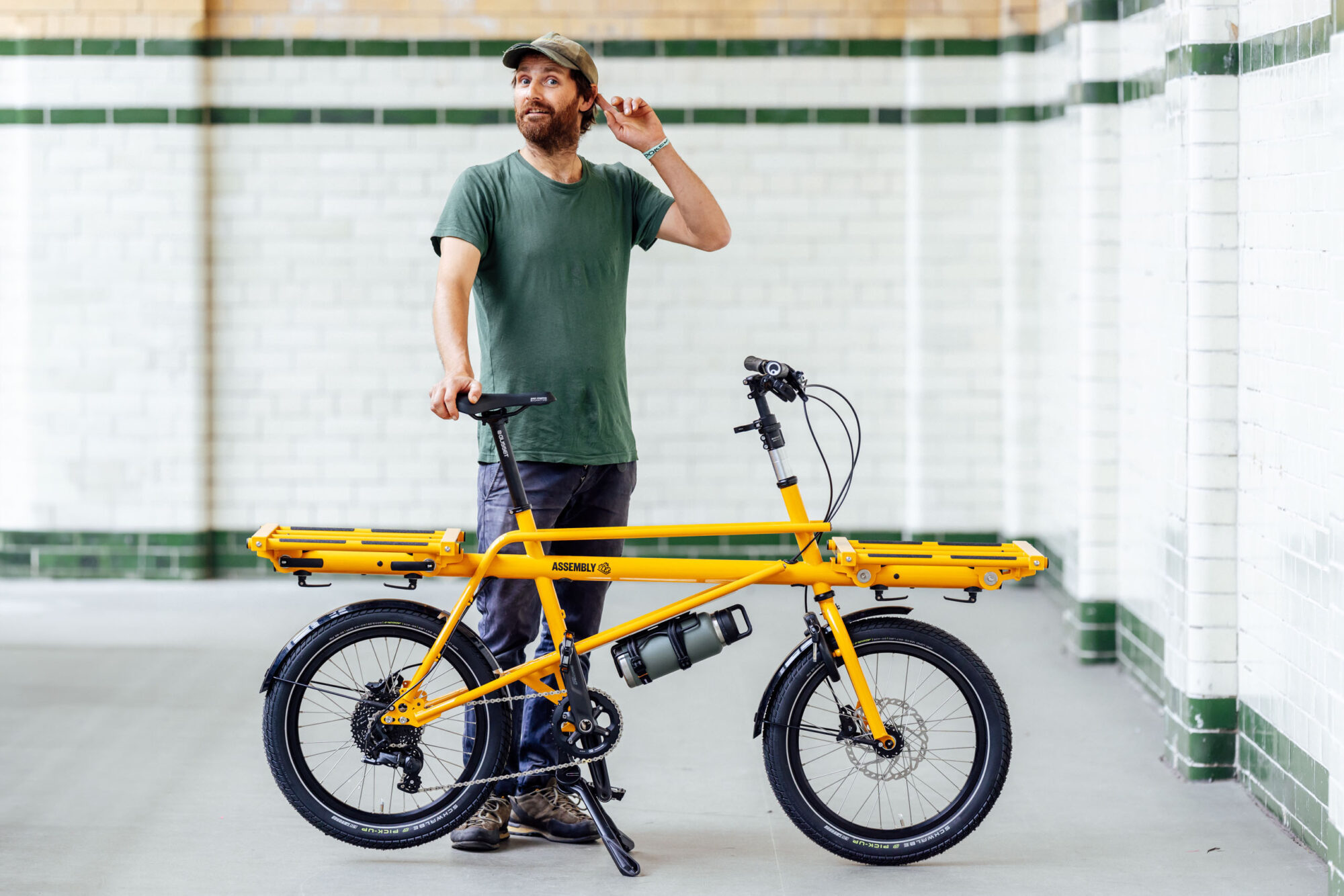
In the early days, Lowe adapted 26” mountain bikes to carry gear. However, about eight years ago, he decided to get more serious about developing a bike specifically designed for carrying cargo. His personal bike even features a sidecar to handle the hefty load he often needs to transport. While he acknowledges that the sidecar might be a hard sell to the general public, he sees great promise in the bike design presented here, which he believes will appeal to customers familiar with traditional diamond-frame bikes. From his conversations with people who have already transitioned to cargo bikes, he learned that the primary pain point is size. Therefore, compact design is a key focus for Assembly, as Lowe believes it is underrepresented in the cargo bike market.
The bike that Lowe designed, and the one I photographed, is referred to as the “Carry Bike.” Assembly plans to standardize this bike model with racks that can be transferable and customized for different needs. These racks may be named according to their function, such as “compact,” “heavy duty,” or “commute,” and Assembly is still ironing out the final designs and prototypes. Lowe prefers the term “carry bike” over “cargo bike” because it conveys a sense of care for what is being transported, whether it’s kids, animals, or other valuable items.
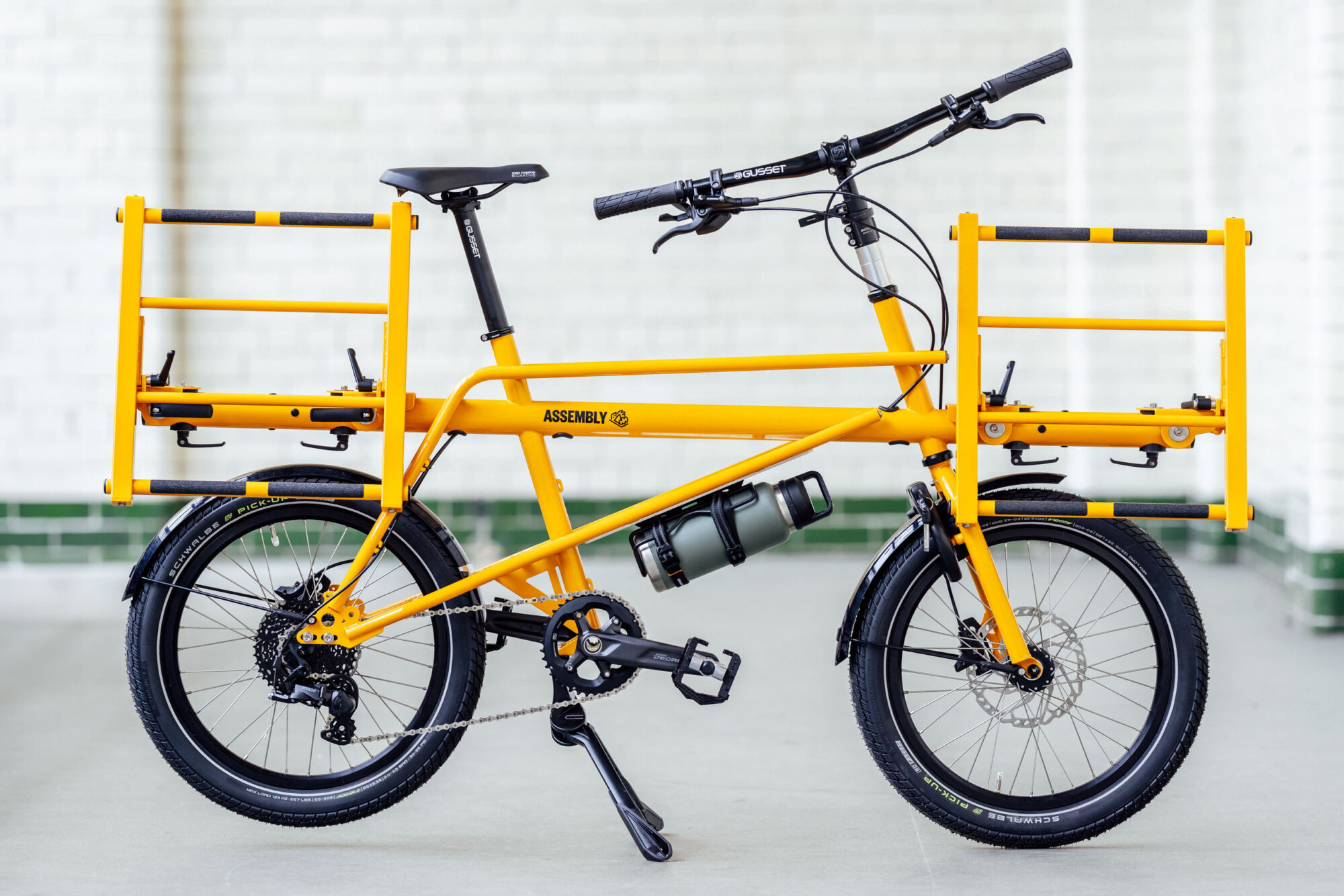
Assembly bikes are all TIG welded in-house using BS T45 tubing, which Jim says offer the right durability and strength. The design is specifically tailored for urban living, a necessity given Assembly’s location in Hackney Wick, East London. Perhaps one of the most intriguing characteristics of the Carry Bike is that it’s compact, measuring just 28cm (9”) in width when the rack and pedals are folded and the handlebars are turned, and 168cm (5’5”) in length. This compactness allows the bikes to be easily stored in hallways of apartments, wedged into small sheds, fitted into elevators, transported on trains, or carried on the back of a car.
Although Assembly is primarily focused on perfecting their Carry Bike and its racks, Lowe dreams of one day releasing the sidecar version to the public. For now, however, the emphasis is on perfecting the Carry Bike to meet the demands of urban cyclists who need a reliable, compact, and versatile bike for transporting various loads.
Lowe’s dedication to creating a practical, user-friendly cargo bike reflects his broader vision of making urban living more convenient and sustainable. The compact design and adaptable construction of Assembly’s Carry Bike is inspiring, and it will be interesting to watch how they continue to develop and prototype new racks to make it more versatile. Oh, and there’s an electrified version, too. If you’re interested in learning more about the Assembly Carry Bike, sign up to be notified on their website or follow them on Instagram @assemblybike.
BTR Fabrications Gasser link
Somerset, England
Midway through day one of Bespoked UK, a common topic of conversation was, “what’s your favorite bike you’ve seen so far?” I heard a few people answer with something like, “the BTR fully is incredibly impressive.” Later that evening during the awards ceremony, BTR Fabrications owner and builder Paul Burford (aka Burf) stood atop a sketchy speaker on the stage to receive the Best in Show award. Obviously, the BTR Fabrications Gasser downhill bike isn’t a bikepacking bike, or even anything bikepacking-adjacent, but it’s pretty impressive and I had to photograph it…
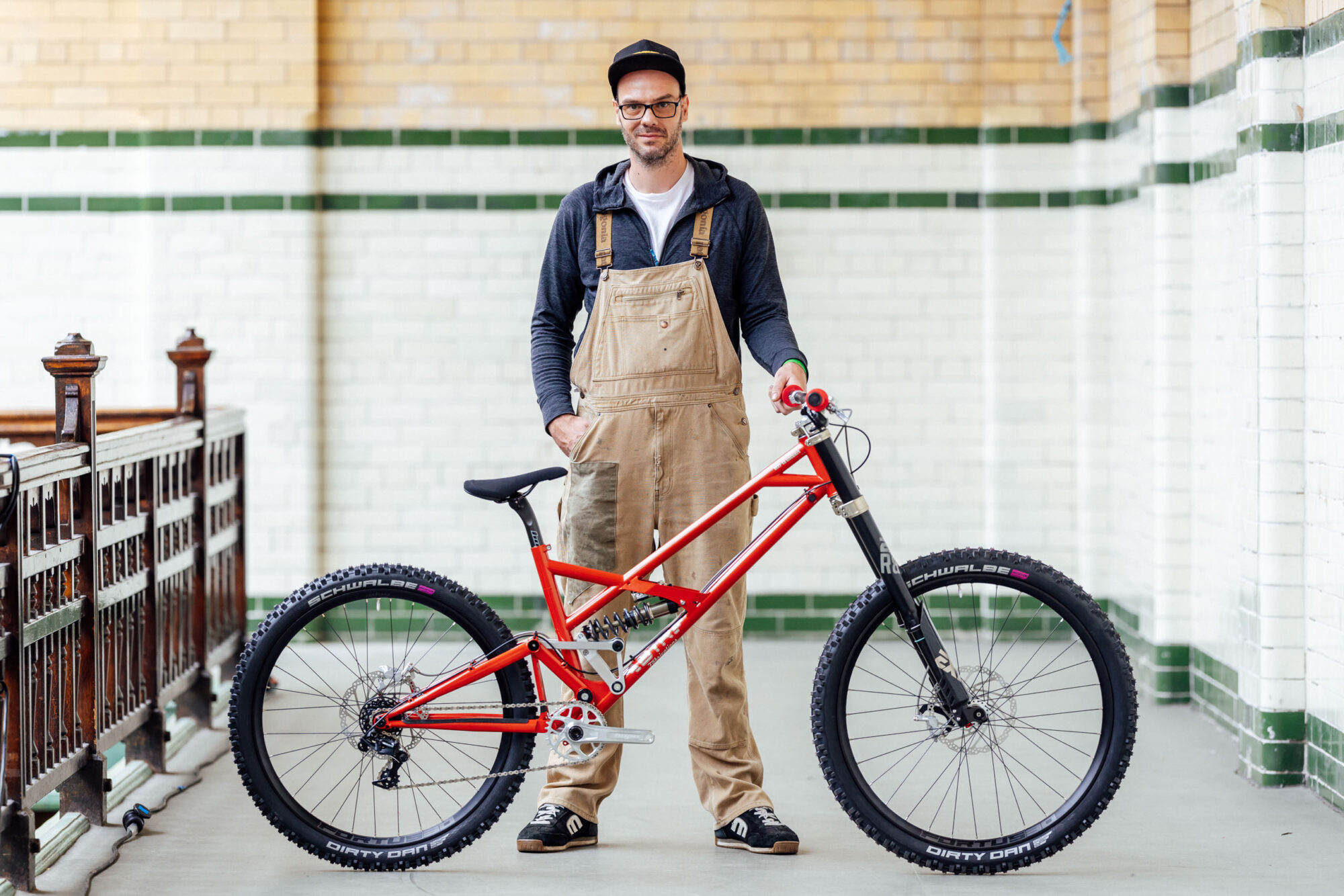
As a teenager, Burford dreamed of owning an MTB brand that made its frames in-house and raced in DH World Cups. Although he raced downhill for a while and aspired to compete in World Cups, the calling to build frames was stronger. He honed his skills as a TIG welder in a sheet metal factory, welding boxes and grinding welds daily. After several other fabrication jobs, he finally felt equipped to create his first frame in 2011, the Belter, a downhill-specific hardtail that marked the beginning of BTR Fabrications. With a 61-degree head angle, 83mm-wide bottom bracket, and a 150x12mm rear axle, the Belter was a bruiser of a bike.
The Gasser, which won Best in Show at the 2024 Bespoked UK Handmade Bike Show, is Paul’s latest creation, a full-suspension downhill bike that’s a thing of engineering beauty and a manifest testament to all-out dedication and craftsmanship. Built for his size—190cm tall (6’3″)—the Gasser features a longer frame, with a fixed 440mm chainstay and a 525mm reach. It’s nothing short of progressive with a mullet 29” front and 27.5” rear tire setup and a 63.5-degree head angle.
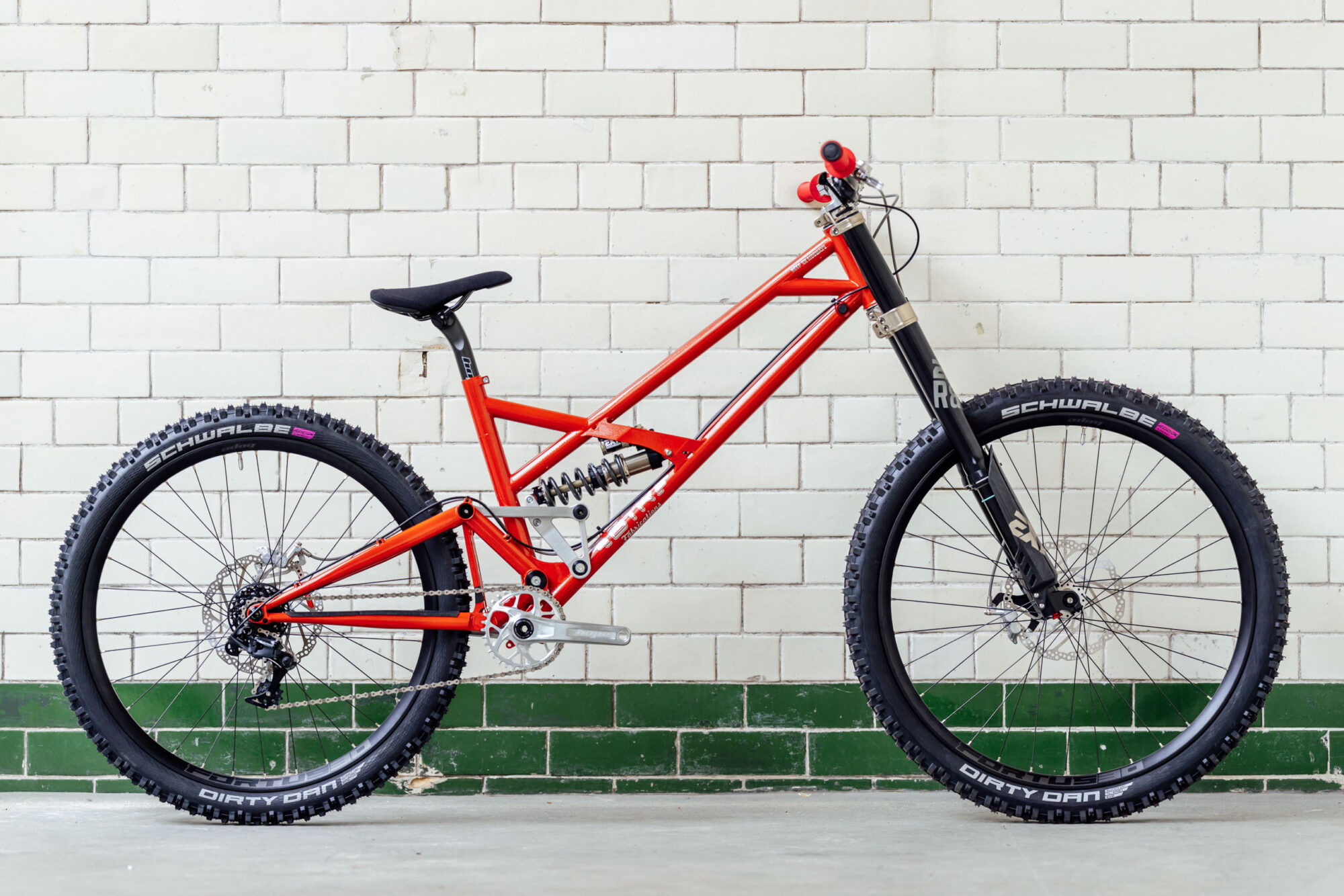
The Gasser has 200mm of suspension up front and 190mm in the back via a linkage actuated single pivot. “The swingarm is single pivot and the damper is actuated by a linkage. The linkage allows me to tune the leverage ratio of the rear wheel forces into the damper,” Paul explains, “So depending on where I put the pivot points I can tweak how easy or how hard it is to compress the suspension, among other things.”
Burf built the frame in its entirety, including the TIG-welded steel tubeset and the machined aluminum linkage swingarm. He’s not sure how long the process took, but looking at it closely, I could only imagine endless late nights under flickering fluorescent lamps in a cold workshop. “I had an order come in for one at the beginning of the year which gave me the excuse to build mine at the same time. I started building both of the swing arms in March ’24 and was filming the process for YouTube,” he explained. He essentially ran out of time and had to finish the customer project and put this bike on hold. “The Gasser’s creation was a challenging journey, and support from Hope, Extreme Racing, SRAM, and Schwalbe was crucial in bringing the Gasser to the show,” Burf described.

Despite his passion for building bikes, Burf admitted financial challenges in sustaining BTR Fabrications. The market for custom-built steel downhill frames is small, making it difficult to make ends meet solely through frame building. To supplement his income, Burf takes on general fabrication work, including unglamorous tasks like rusty car and van repairs. “Laying on the floor in January under a van on axle stands with molten metal landing on your chest is pretty grim,” Burf lamented. However, he remains committed to his dream of building unforgettable bikes that provide unforgettable experiences. He mentioned aspiring to build more DH bikes and perhaps more process filming for his YouTube channel, and he’s at the idea stages of making a dedicated bikepacking rig with integrated features, a concept that I can’t wait to see.
As BTR navigates the challenges of the custom bike market, Burf’s story serves as a reminder of the passion and perseverance behind every handcrafted frame. That makes me think of the quote from Pi I reference in the intro. If you’re interested in seeing more of the Burf’s creations, check out his website and give him a follow on Instagram @btr_fabrications. You can also check out his YouTube channel and follow him there, too (he’s hoping that behemoth will monetize him at some point).
Collins Cycle Works link
South Staffordshire, England
Amidst the impressive handmade bikes at Bespoked UK, there were a few booths featuring other small makers showing off their wares. Collins Cycle Works caught my eye, for obvious reasons. After all, it’s hard to ignore colorful, hand-stitched X-pac bags in my line of work. However, upon further inspection, there were a lot more to Collins’ bags than I expected…
The brand’s proprietor, Patrick Collins, affectionately known as “Patch,” began making bags in 2019 as a side hobby after a good friend sent him a photo of a bike setup for bikepacking. Intrigued by the potential of custom bike bags, he dove in head first. Today, he operates out of a modest 140-square-foot shed in Kinver, a small village at the bottom of South Staffordshire in central England. The environment surrounding Kinver is rich with bridleways, byways, and poorly maintained country roads, or “British Gravel,” as Patch calls it. “So you’re never far from rattling your teeth out or being a foot deep in mud or water. Plus, it rains a lot here,” Patch explains. These positively British riding conditions drives him to make bags that are squeak/rattle-free and 100% waterproof. So my question was, “how so with stitched bags?” As many of you know, stitching and waterproofness don’t go hand in hand.
One of the unique features of Patch’s bags is that each has an internal welded TPU liner. This innovation was born from all the aforementioned ridiculousness that the English subject themselves to. “If it’s not sunny here, it’s raining. Who wants wet kit when they turn up to camp? I didn’t…” he notes. Seeking an aesthetically-pleasing solution, he combined the external look of sewn bags with the waterproof capabilities of welded bags, using an interior TPU nylon fabric that he could weld himself without expensive machinery. This ingenious approach allows his bags maintain that stitched look while providing protection from the elements.

The first bag Patch made was a half-frame bag built from brown Cordura with sewn-in Velcro straps and a bright orange logo. Reflecting on it, he laughs, “It was an awful-looking thing.” However, this initial attempt laid the foundation for his future designs. Among his creations, the HipRoll stands out as his proudest achievement. This hip pack has morphed through several iterations (now at version 3), incorporating Fidlock connectors, a Fidlock bottle attachment, a waterproof liner, and eco-friendly recycled Ecopak fabric. Patch is confident in it, stating, “The world’s best hip pack? Maybe.” I was pretty impressed in person and would be keen to put one to use with a camera.
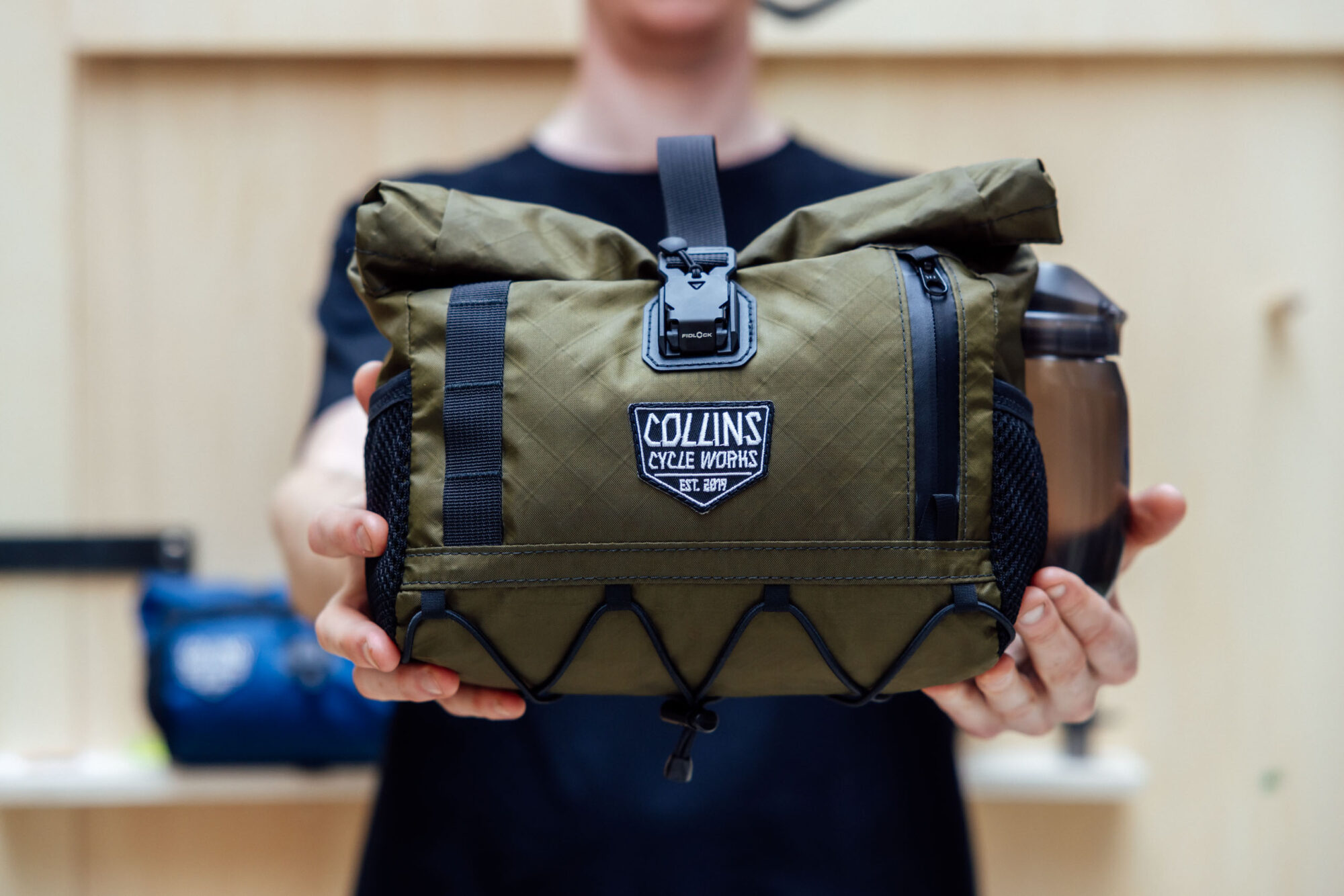
Patch’s workshop in his parents’ garden is home to four sewing machines at this point, and he’s also “borrowed” their garage to make his own racks and store his bikes. Oh yeah, he recently made a pretty cool rack he had on display, too, which was built specifically for another one of his products that I was especially impressed by: these small panniers. Constructed like his other bags, they each have a welded internal liner and use a clever combination of a fiberglass strut and Hypalon to strap them onto the rack. Public note to BIKEPACKING.com editors: add these to the Mini Panniers Gear Index ASAP.
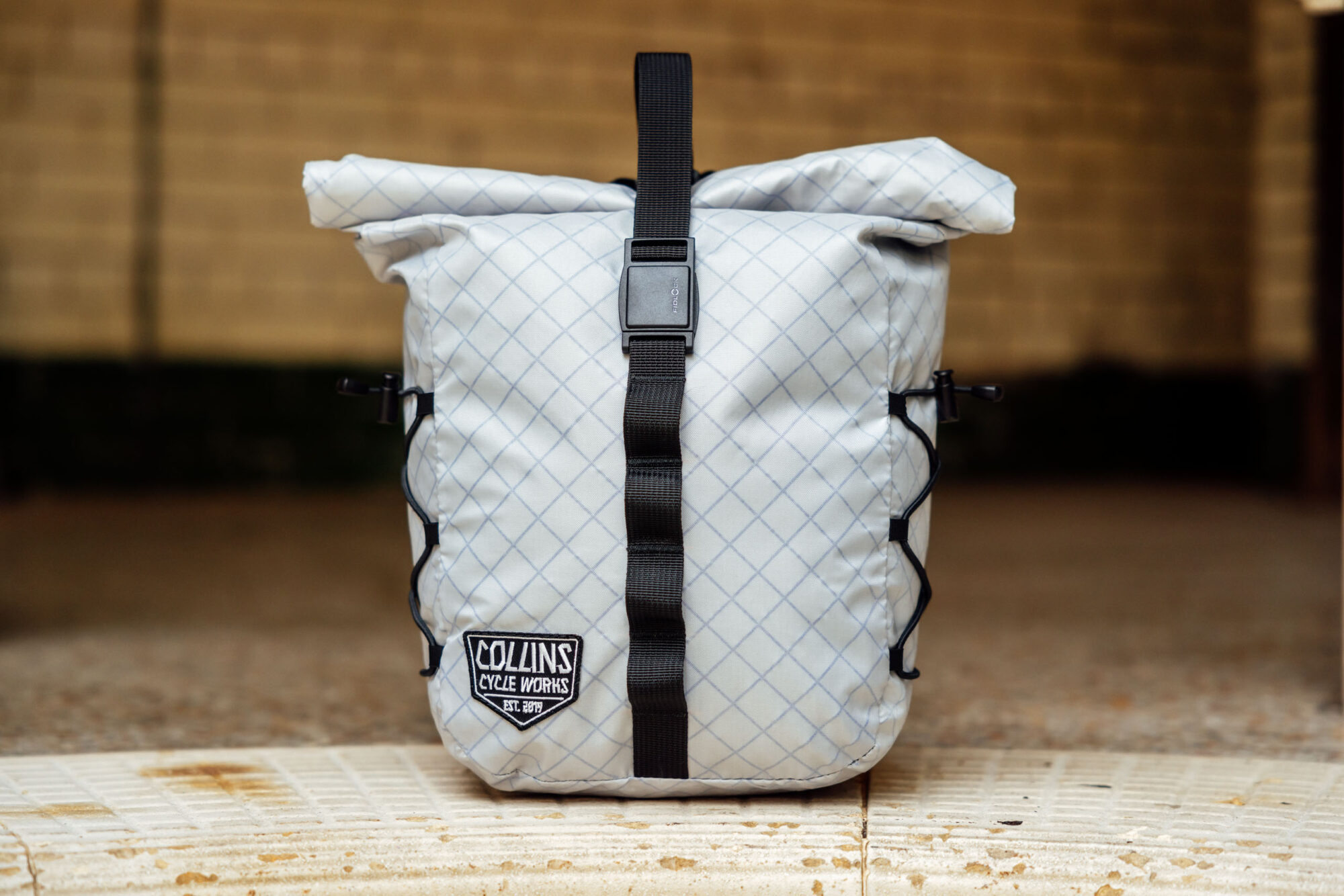
With Bespoked UK behind him, Patch is currently scheming some interesting rides. He has his sights set on a four-day trip from home, looping around the Trans Cambrian Way and back. Additionally, he plans to tackle the 100-mile way-marked bridleway called the 3 Rivers Ride, which runs from Bromyard in Herefordshire to Brecon in Wales. Looking to next year, he hopes to embark on a 10-day adventure along the west coast of Ireland, a journey that will undoubtedly put his waterproof bags to the test. Further ahead, Patch plans to keep improving his products and find ways to reduce plastic usage in his designs. He’s also considering expanding into a line of lifestyle and wearable items, including backpacks. To learn more about Collins Cycle Works’ products, head to the website here, and be sure to give them a follow on Instagram @collinscycleworks.
TWMPA AR-1 link
Hay-on-Wye, UK
The AR-1 wooden bike by TWMPA captured the attention of many curious passers by, including mine. I admit that I’ve kind of glossed over wooden bikes in the past, but the AR-1 was hard to ignore. The founder of TWMPA, Andrew Dix, told me a little more about this bike and how it’s made, including the fact that it’s constructed from CNC-machined hollow tubes, which was slightly mind blowing.
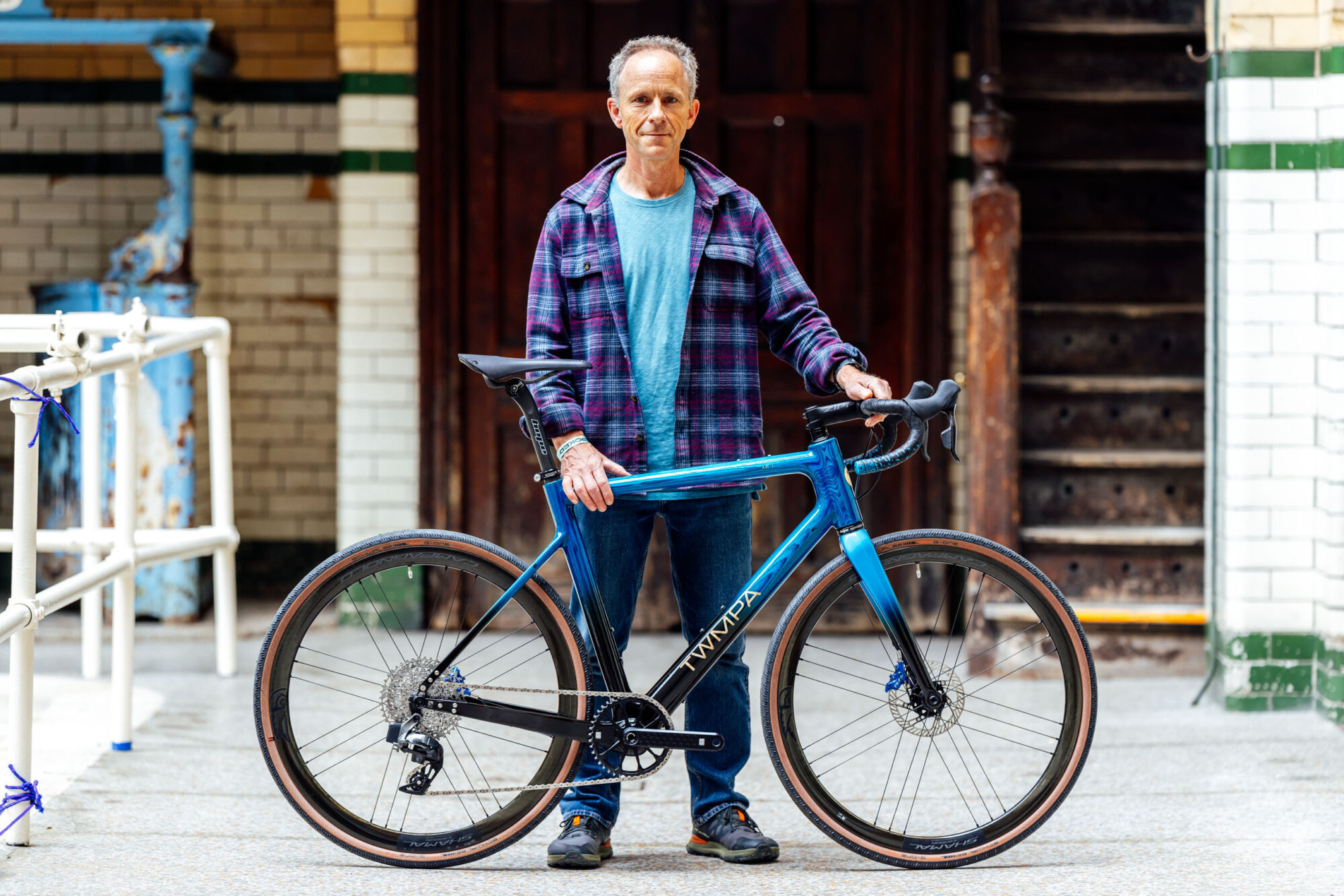
After working in various engineering roles, Andrew set up his own furniture business in 2003. A chance conversation with Rob Penn, the author of “It’s All About The Bike,” sparked the idea of building a wood-framed bicycle. This venture began as a personal project and, to Andrew’s surprise, turned out to be a success. “Those who have ever had this experience will understand my surprise when the entire thing didn’t immediately revert to a pile of sticks, and my further elation when it actually turned out to be rather nice to ride,” he recalls.
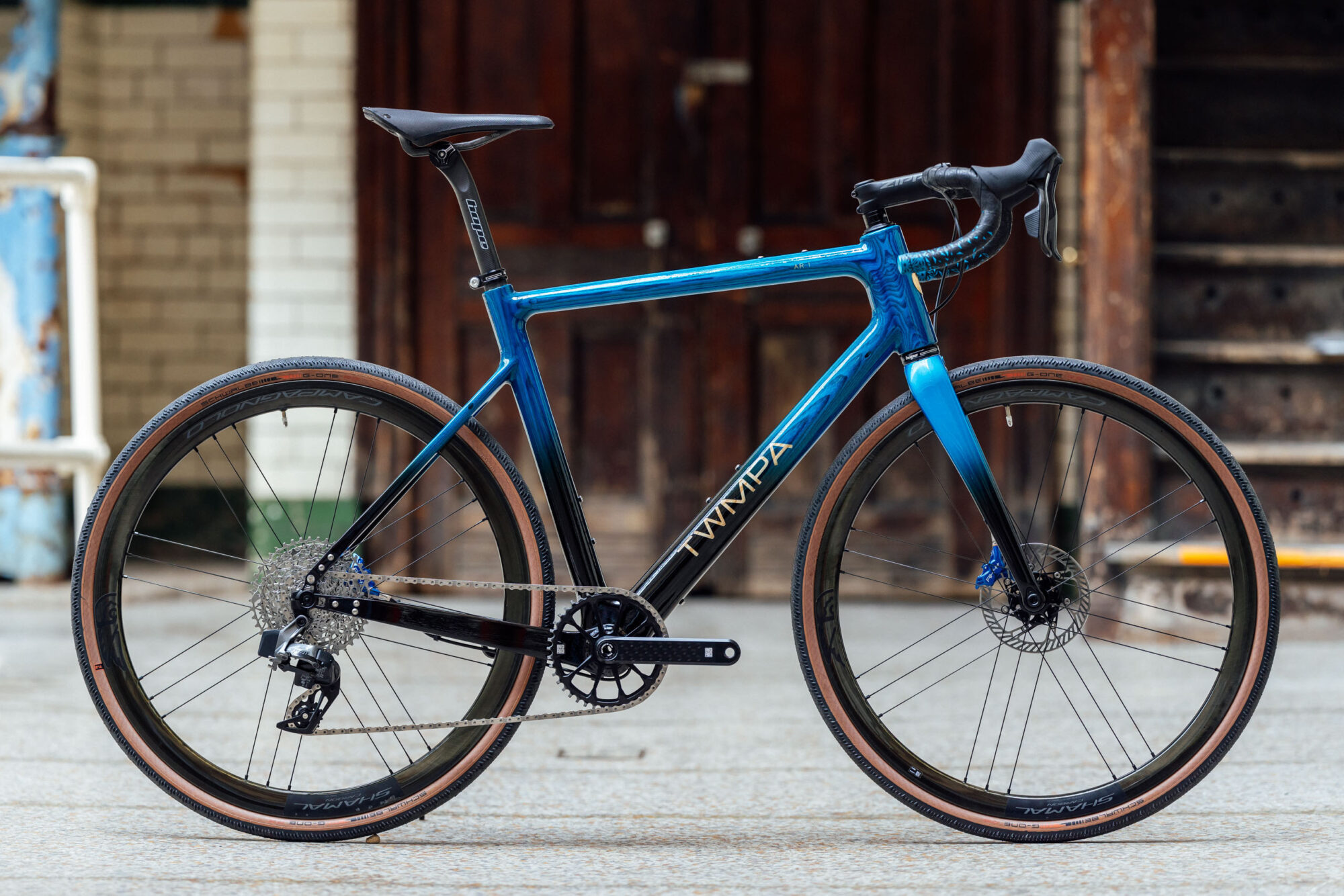
That first wooden bike frame attracted attention and commissions, pushing Andrew further into the world of bike building. His curiosity led him to delve into timber material science, learning about different woods’ natural shock-absorbing properties and how to leverage them for bike frames. This meandering journey also saw him mastering 3D parametric CAD modeling and modern CNC machining, and even taking a crash course in bike geometry with Tom Sturdy at the Bicycle Academy.
The name TWMPA is derived from the mountain behind Andrew’s home base in Hay-on-Wye, on the Welsh borders. This hill is also known as Lord Hereford’s Knob, which Andrew humorously notes wouldn’t fit on the downtube. The area around TWMPA features everything from narrow, car-free lanes to rugged mountain bike trails, all of which have significantly more elevation changes than a lot of the UK. Andrew mentioned that this is a contributor to he preference for mullet gravel drivetrains, combining drop bar cockpit components with mountain bike derailleurs and cassettes.

The AR-1, TWMPA’s all-road geometry bike, represents the culmination of Andrew’s work up to this point. That includes his experience as a furniture maker, which provided a deep understanding of how grain orientation and joinery can eliminate points of failure. The frame is CNC-machined, a process that Andrew adopted for its precision and efficiency. “Firstly, I knew I needed to be able to manufacture relatively quickly, with consistent, repeatable high quality. Where a tube is designed to have a wall thickness of 4mm, it needs to be just that, and not closer to 5mm or 3mm,” he explains. He says this precision ensures the optimal balance between weight and strength. I was honestly shocked when I picked up the AR-1 and felt how light it was. It’s made of Ash wood, in case you were wondering. Its weight wasn’t too dissimilar from an alloy bike.
For more on TWMPA and their bikes, head over to their website here and you can see more on Instagram @twmpacycles.
We’ll be back this week (hopefully tomorrow) with a whole lot more from Bespoked UK. Stay tuned! In the meantime, you can dig into past coverage from previous years at #bespoked.
Please keep the conversation civil, constructive, and inclusive, or your comment will be removed.