Tight Tolerances: A Field Trip to DT Swiss
Ever wondered how DT Swiss makes their spokes, adds graphics, or builds their wheels? Well, you’re in luck. Neil took a field trip to their North American facility last month, where he got the inside scoop on all that and more. Find the video tour and photo gallery here…
PUBLISHED Nov 9, 2024
When Brandon, the Marketing Manager at DT Swiss, invited me to visit their space this fall, I was beyond excited to see where the magic of the storied brand comes together. Located just up the road in Grand Junction, I figured it was a good excuse to escape the higher elevations of Colorado in October.
Upon arrival, it was pretty clear that the facility in Grand Junction was more than just a warehouse. There were sales and marketing teams, wheels being built, decals being applied, and even spokes being made. After a full tour of the facility, an in-depth look at how many of the DT Swiss products we’re familiar with are made, and an overnighter with some of the folks at the factory, I got a relatively complete picture of what goes on at the US-based DT Swiss facility. Watch the video tour below and scroll on for a written version with photos from my time there.
History of DT Swiss and its facilities
DT Swiss, founded in 1994 in Biel, Switzerland, just celebrated its 30th anniversary. Although the company initially focused on building high-quality spokes, its reputation for precision and durability quickly laid the groundwork for expanding into other components, eventually branching out into hubs, complete wheels, and suspension systems.
One of the innovations that put DT Swiss on the map was their Ratchet System hub. The design changed the game for hub reliability by blending durability, simplicity, and smooth operation, inspiring a number of designs currently seen on the market. By the 2000s, they expanded globally, setting up production facilities across Europe, Asia, and North America. As of 2024, they manage seven facilities worldwide, each churning out a range of components. While DT Swiss mainly supplies OEM wheels to bike brands worldwide, they’ve become a top choice for custom wheels built by bike shops and home mechanics all the same.
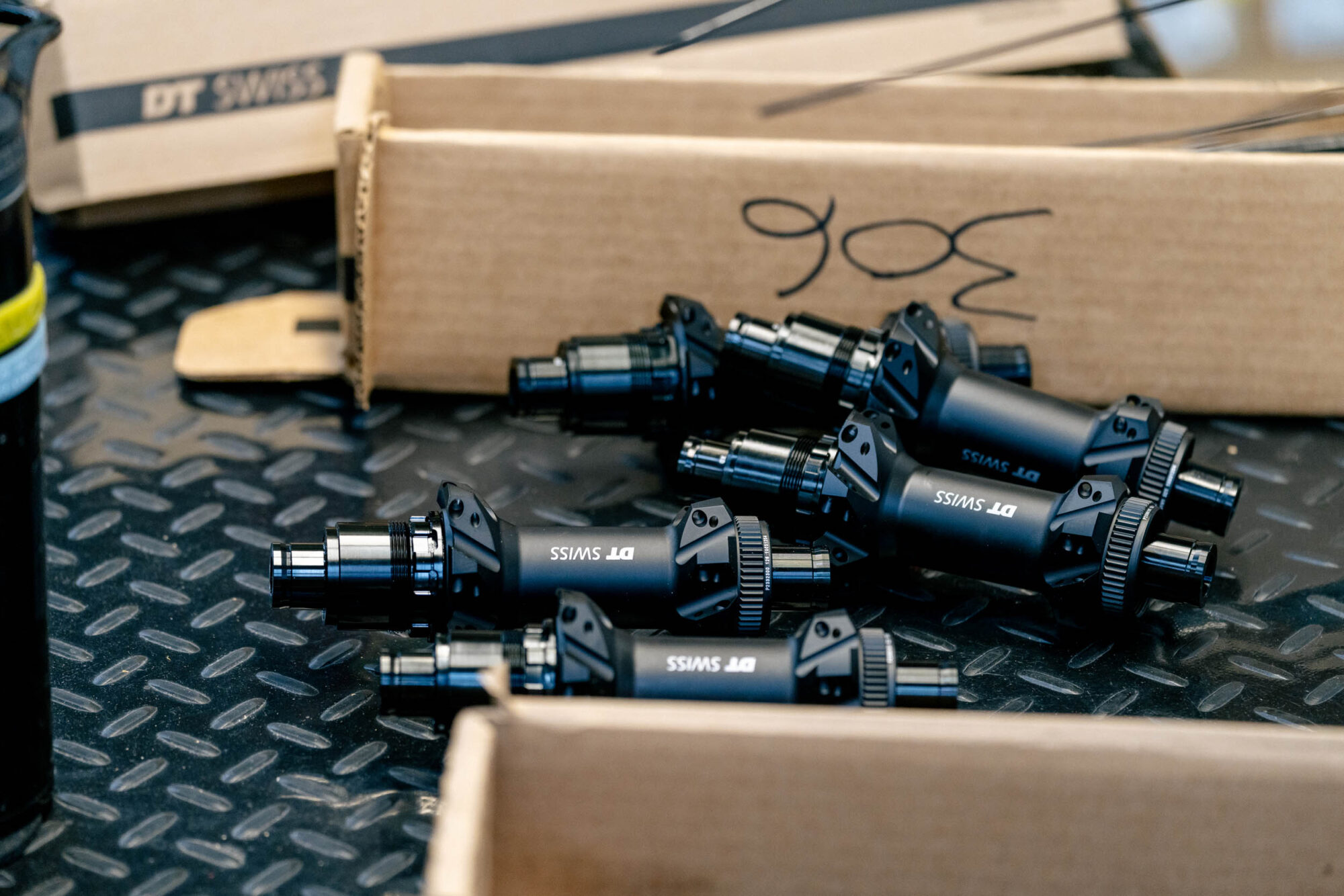
Though the sheer number of SKUs still feels like a lot to take in, visiting their facility helped me better understand their hub systems and spokes while also instilling a newfound respect for their craftsmanship. DT Swiss takes pride in making well-built, high-quality parts, and I witnessed why that’s important at their facility in Grand Junction.
DT Grand Junction
The facility itself is pretty impressive. The large warehouse is stocked with a ton of wheels and the necessary components for the building process, such as freehub bodies, end caps, spokes, rims, hubs, and more. While bladed and hybrid spokes are imported directly from Switzerland, I was surprised to learn they make straight-gauge and round-butted spokes right there in Grand Junction.
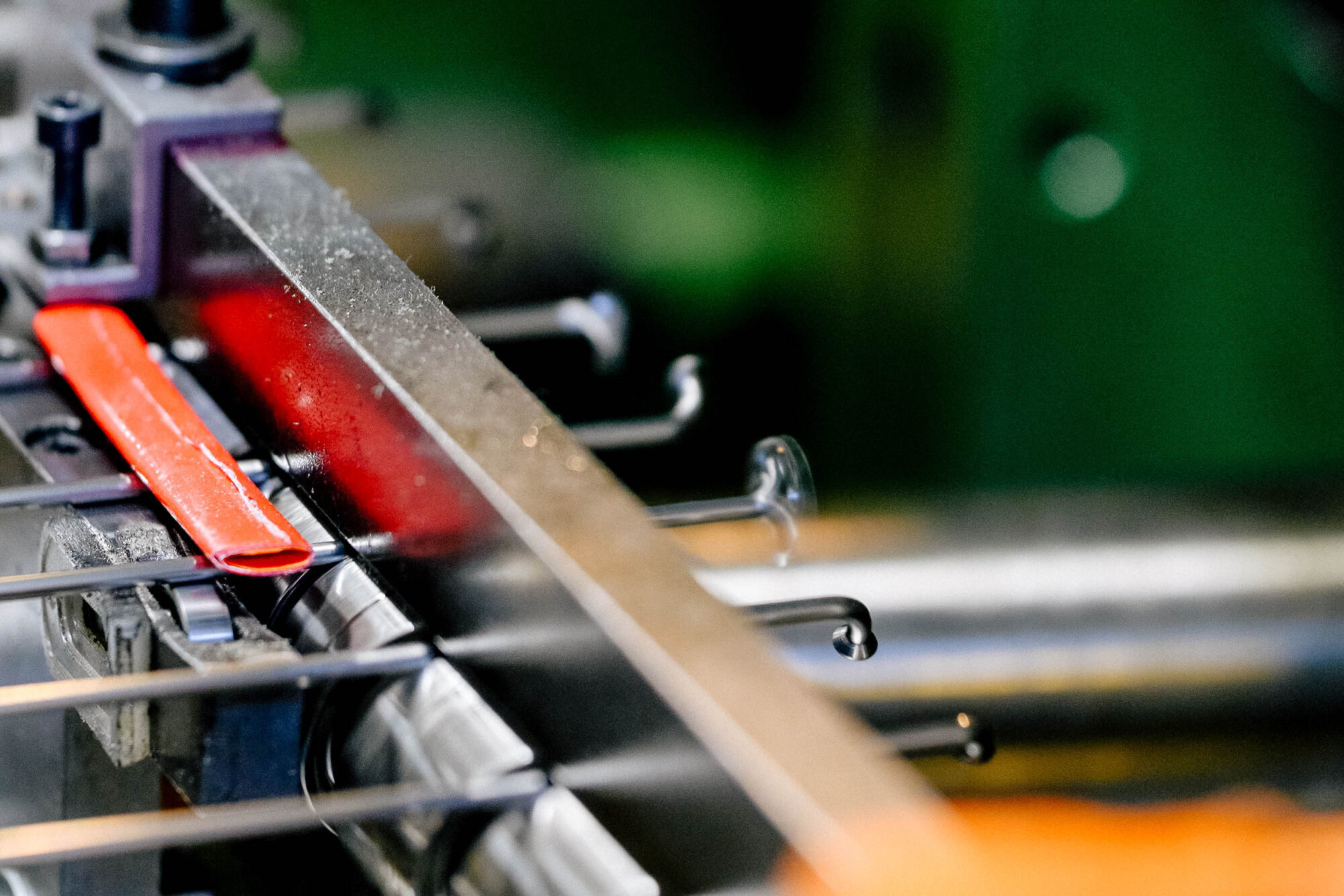
Stepping into DT Swiss’s spoke production area, I was awestruck. Witnessing the production process of spoke-making entranced my bike-obsessed mind. They start with 2mm wire fed from massive spools into spoke-making machines, which then cut the wire to specific lengths set by the technicians, keeping some as blanks and threading others. The threading process uses machines that expand the spoke diameter with super-tight tolerances, ensuring each spoke fits perfectly.
After inspection, some spokes are blackened, while others remain silver. The spokes are then sorted by color and packaging and sent back to the warehouse, where they are either shipped out as individual spokes or built into wheels. All the wire is sourced from a sole European supplier, ensuring uniformity across DT’s global facilities. With primarily German-made machines, the process remains consistent worldwide, and experienced technicians make sure everything runs smoothly.
Another one of the in-house tasks is decal placement on all the rims. It’ a surprisingly interesting process to see live. For DT rims, especially the carbon ones, decal placement is all about careful prep and precision. Before applying, the surface is lightly abraded for better adhesion and then cleaned again to ensure no leftover debris. After a thorough cleaning, the water slide decals go on—a namesake derived from how they slide off the backing sheet when exposed to water, allowing easy application onto the rim.
Once the decals are positioned, a carrier foil holds it all together. After an initial low-temp bake to set the decals, they peel off the foil and check for any bubbles, debris, or misalignment. If it’s all looking good, the rims go through a second, higher-temp bake that locks decals in place, keeping placement tolerances super tight–around 1.5mm. A bit of heat during application also helps to smooth out bubbles and get that perfect finish. After one last quality check, the rims are returned to the warehouse.
Wheel Building
The primary function of DT Swiss’ North American facility is to support wheel building and provide services for bikes and brands assembled in the USA. So, if your bike was built in the U.S., there’s a solid chance the wheels were made in Grand Junction. Here’s how it works: their rims, hubs, and spokes sit in a warehouse staging area until they get a production order—usually from bike brands like Otso or Pivot, for example. Each order specifies the quantity, components, lacing pattern, and other details.
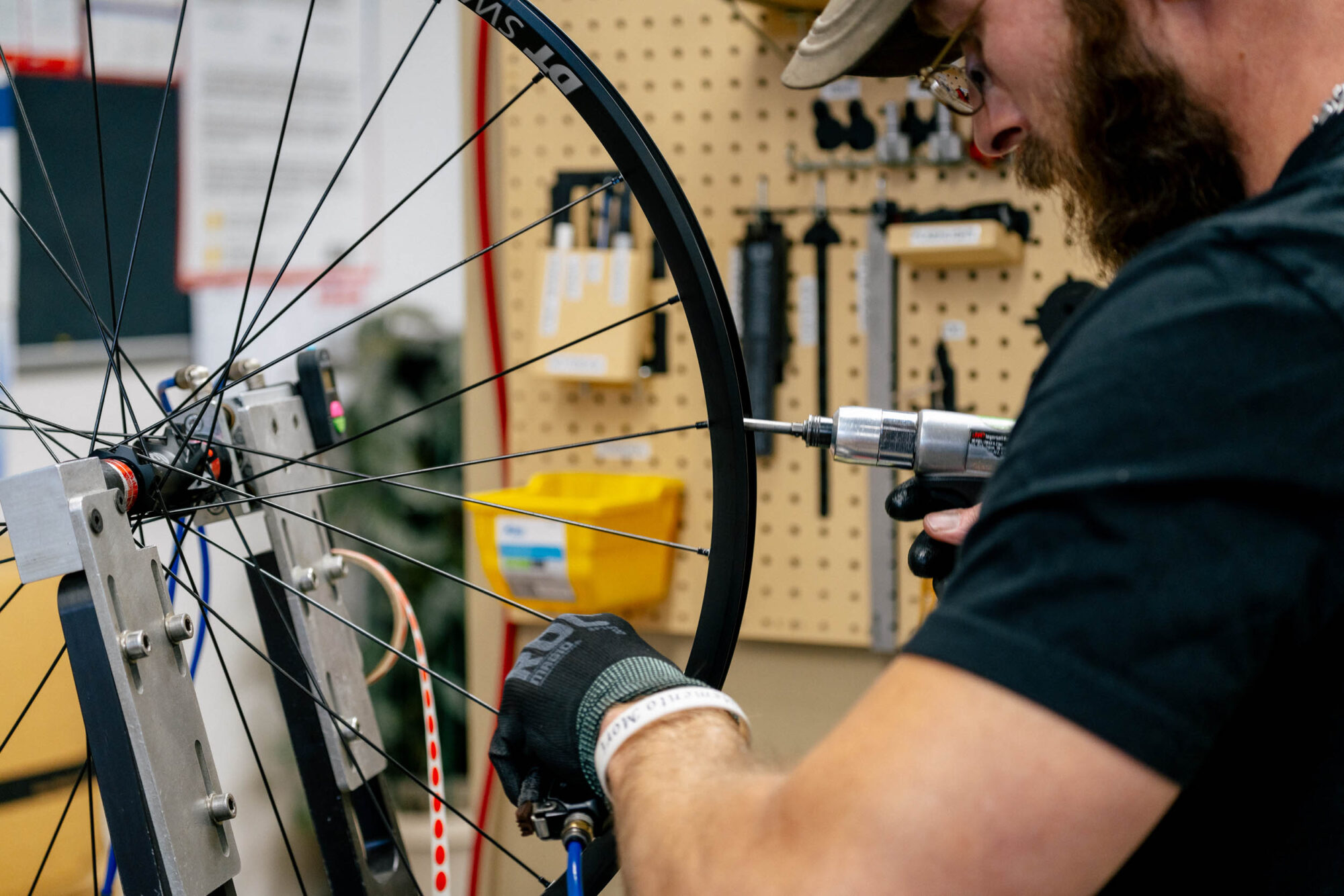
A technician starts the lacing process after the hubs arrive fully assembled from Taiwan or Poland. The laced hubs then stack on top of each other, creating what they call the “Christmas tree.” Once the tree is full, it’s moved to the lacing machines. DT Swiss uses these machines to streamline the wheel assembly process, saving quite a bit of time. While hand-lacing is labor-intensive and doesn’t add much in the way of quality, these machines make the process efficient. But the interesting thing here is that the machine doesn’t apply tension to the wheel. It simply sets the wheel builder up with loose spokes, ready for the tensioning process.
After the tension-less wheel comes off the lacing machine, it moves on to someone who handles the tensioning. DT Swiss uses pneumatic screwdrivers with controlled drill bits to streamline this part of the process, ensuring consistent threading of nipples onto spokes. These tools bring spokes up to about 60 to 85 percent of the required tension. Usually, manually building and truing a wheel can take around two hours, but DT Swiss’ streamlined process cuts it down to just about five minutes. The remaining 20 percent is handled by a skilled truer—an experienced, vetted technician who can crank out over a hundred wheels daily.
DT Swiss considered automated truing machines but found their experienced technicians more effective. The automated machines are not only costly and require maintenance, but DT’s staff—many of whom have over a decade of experience—can true wheels faster and to a higher, more cost-effective standard.
Once the wheels are fully trued, they’re rolled into another room on the same racks they’ve been on since the initial lacing process. This is where DT Swiss uses a de-stressing machine, a hydraulic press that applies controlled force to the spokes without damaging the hub. With a hollow center, the press avoids putting excess pressure on the internal hub components. The machine is pre-programmed with different air pressures, allowing it to adapt to various spoke types, applying lighter pressure for bladed spokes and higher pressure for round spokes. Each wheel undergoes this de-stressing process three times on each side, ensuring the spokes are properly stretched and tensioned.
After de-stressing, the builder places the wheel back on a truing stand to assess its balance, run-out, and alignment, comparing it to others in the order. They start by correcting any imbalances and centering the wheel. Then, the wheel goes through another de-stressing cycle, fine-tuning the dish. Once alignment is dialed in, the wheel is brought up to 100 percent tension, ensuring optimal performance and durability.
Though DT Swiss didn’t share specific measurements, they use highly precise gauges to track wheel movement, measuring both lateral and vertical shifts down to hundredths of a millimeter. This level of precision achieves a smoothness beyond typical bike shop standards, especially with naturally flatter carbon wheels. And while these gauges allow for fine tolerances, it’s often the technician’s expertise that catches the most subtle adjustments. Spoke tension is also regularly checked using a tension calibration unit, where a weight is attached to a spoke to ensure the ideal tension. DT Swiss uses separate calibration tools for bladed and round spokes to keep the tension tool perfectly dialed in.
After de-stressing, the wheels are placed back on racks, leave the de-stressing room, and move to the quality and packaging room. There, each wheel undergoes precise inspection with digital gauges linked to a computer, feeding data directly into a centralized database accessible across all DT Swiss’ global facilities. This system ensures consistent quality and coordinates quality and non-quality wheels to a green and red system. If a wheel receives a red, no-go rating, the wheel will go back to the previous wheel builder with a note detailing the issues.
For a wheel to leave the facility, its dish and tension must pass rigorous inspection and recording. This data is logged and stored for years, offering a detailed record invaluable for verifying product specifications when needed. This meticulous tracking helps DT Swiss maintain quality and avoid potential issues while also ensuring reliability and accountability for their customers. The process of each wheel build is fully traceable throughout the production process, with detailed records of each person who handled it. Stickers on the wheels identify who drilled and trued them, creating a clear feedback loop between quality control (QC) and the builders.
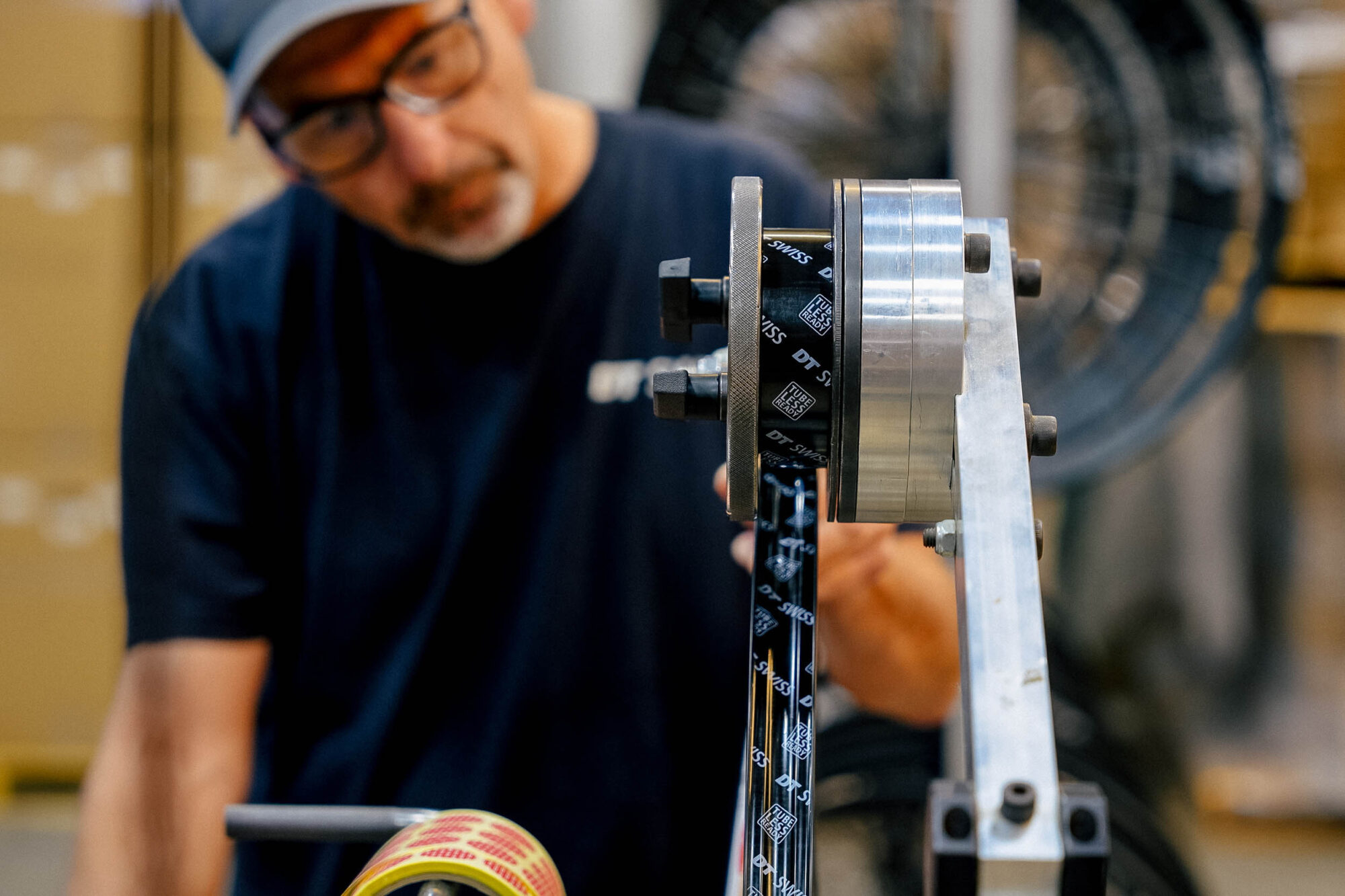
After inspection, the wheels move to the taping stands. These stands hold the wheels perfectly still, allowing technicians to apply tubeless tape accurately. The process is more challenging than one might imagine, as the tape must be carefully aligned to avoid shifting too far to one side, compromising tire mounting. DT Swiss overlaps the tape by four to six inches and uses rim tape two to three millimeters wider than the inner rim width, ensuring a snug fit that fills the rim channel.
After the taping process, DT Swiss wheels undergo a final inspection and cleaning. Strong alcohol removes any remaining machine oil or residue, ensuring the wheels are spotless. This step includes a thorough visual inspection to check for scratches, flaws in the rims, damage to hubs, or issues with spokes. This last comprehensive review provides the chance to catch any imperfections. Once the wheels pass their final inspection, they’re packed for shipping. Depending on the order, they are either placed in a six-pack box for OEM customers or individual boxes for smaller customers.
It’s worth mentioning that DT Swiss places a laser-printed ID label with a QR code on each wheel. By scanning this code or entering it on the DT Swiss support page, customers can access detailed information about their specific wheel, including part numbers, upgrade options (like switching to Micro Spline or updating ratchets), and details like spoke type and weight. This feature simplifies tech support and product upgrades, making it easier for users to manage and maintain their wheels, and helps DT Swiss identify counterfeits.
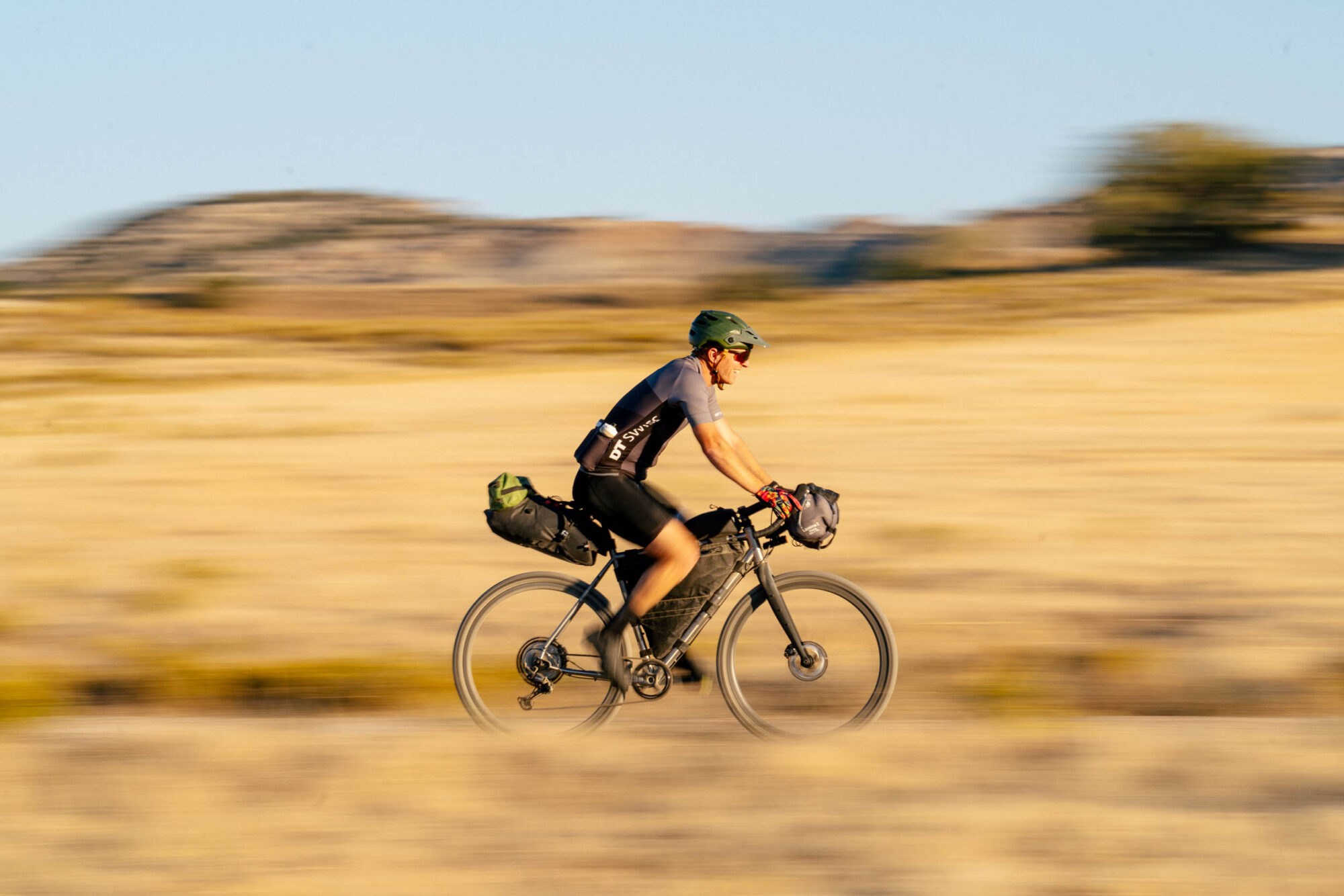
Final thoughts
So, there you have it, the DT Swiss North America facility. You saw the nuts and bolts of the operation, but there are plenty of other moving parts, like the warranty and service departments, marketing garage, office spaces, and, of course, their backyard, which we explored on an overnighter. I had a blast getting to know the team, their passion for wheels and bike components, and their love for being out on the bike.
Further Reading
Make sure to dig into these related articles for more info...
Please keep the conversation civil, constructive, and inclusive, or your comment will be removed.